/competitions
roll over images for information

The airy white pavilion consists of 585 interlocking components made of plant-based bio plastics, printed over 10,800 hours, mimicking the look and feel of its setting in a redwood forest. Measuring 10x10x8, the structure was assembled in four days. The bioplastics will enable the pavilion to eventually decompose naturally within the forest, just like the trees that grow all around it. 1

The airy white pavilion consists of 585 interlocking components made of plant-based bio plastics, printed over 10,800 hours, mimicking the look and feel of its setting in a redwood forest. Measuring 10x10x8, the structure was assembled in four days. The bioplastics will enable the pavilion to eventually decompose naturally within the forest, just like the trees that grow all around it. 2

The airy white pavilion consists of 585 interlocking components made of plant-based bio plastics, printed over 10,800 hours, mimicking the look and feel of its setting in a redwood forest. Measuring 10x10x8, the structure was assembled in four days. The bioplastics will enable the pavilion to eventually decompose naturally within the forest, just like the trees that grow all around it. 3
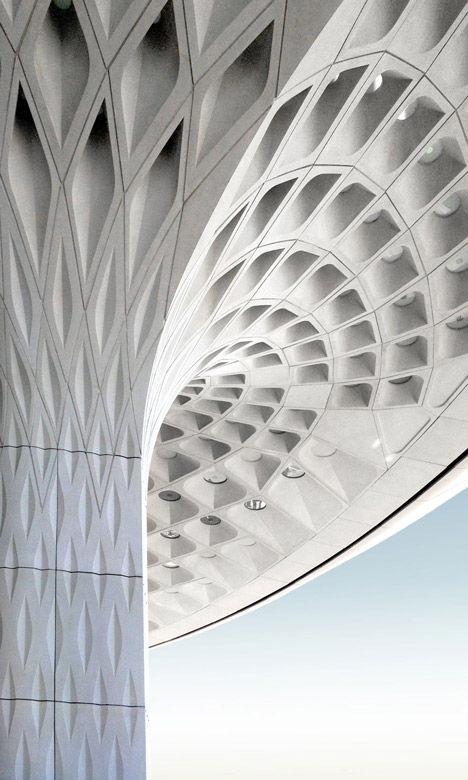
This canopy is supported by 30 tapered columns that are punctured with similar recesses, creating a decorative pattern of openings that are infilled with coloured glazing to allow light to filter through the space. 4
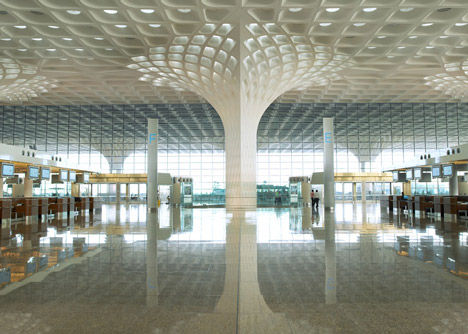
This canopy is supported by 30 tapered columns that are punctured with similar recesses, creating a decorative pattern of openings that are infilled with coloured glazing to allow light to filter through the space. 5

This canopy is supported by 30 tapered columns that are punctured with similar recesses, creating a decorative pattern of openings that are infilled with coloured glazing to allow light to filter through the space. 6

The 3D-printed sheaths were designed during a competition to surround a series of complex joints between columns and a web of arms that support the canopy's EFTE plastic roof. The components were subjected to rigorous environmental testing before being included in the warranty for the roof by EFTE specialist Vector Foiltec, which was responsible for the installation of the canopy.

The 3D-printed sheaths were designed during a competition to surround a series of complex joints between columns and a web of arms that support the canopy's EFTE plastic roof. The components were subjected to rigorous environmental testing before being included in the warranty for the roof by EFTE specialist Vector Foiltec, which was responsible for the installation of the canopy.
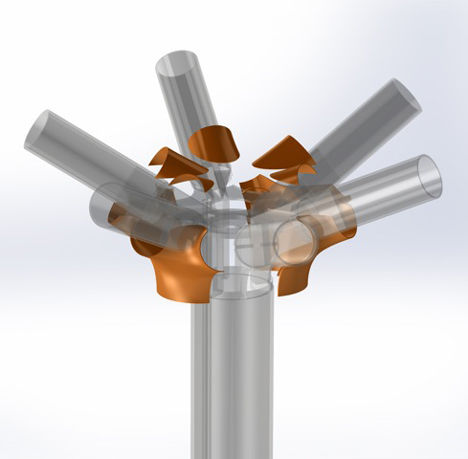
The 3D-printed sheaths were designed during a competition to surround a series of complex joints between columns and a web of arms that support the canopy's EFTE plastic roof. The components were subjected to rigorous environmental testing before being included in the warranty for the roof by EFTE specialist Vector Foiltec, which was responsible for the installation of the canopy.
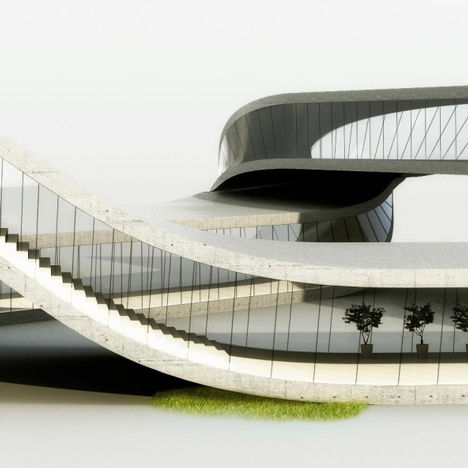
The Landscape House will be printed in sections using the giant D-Shape printer, which can produce sections of up to 6 x 9 metres using a mixture of sand and a binding agent.

The Landscape House will be printed in sections using the giant D-Shape printer, which can produce sections of up to 6 x 9 metres using a mixture of sand and a binding agent.

The Landscape House will be printed in sections using the giant D-Shape printer, which can produce sections of up to 6 x 9 metres using a mixture of sand and a binding agent.